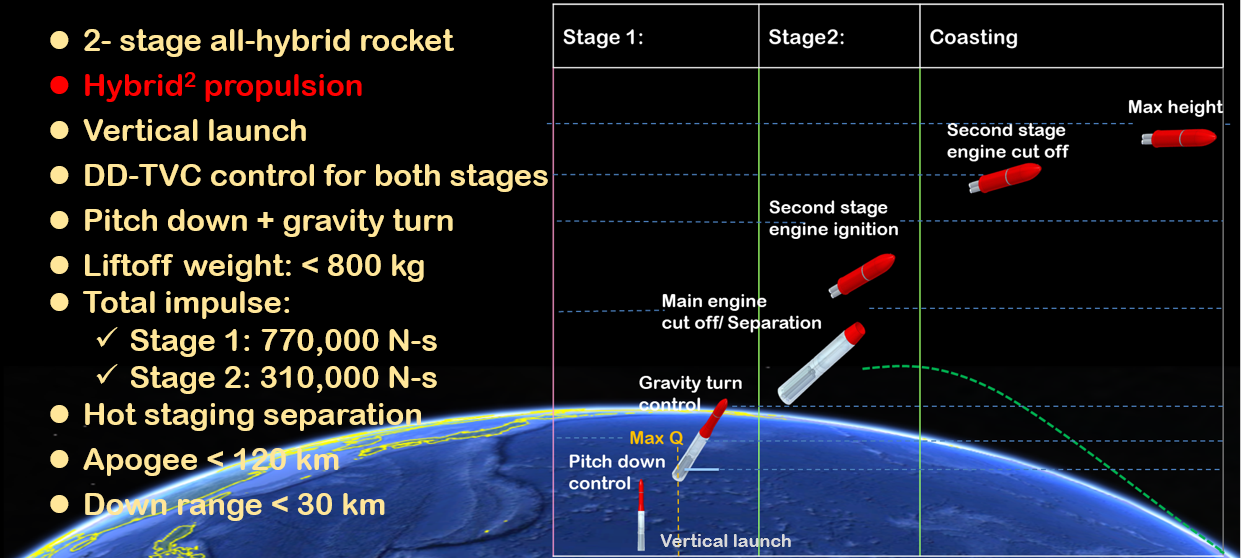
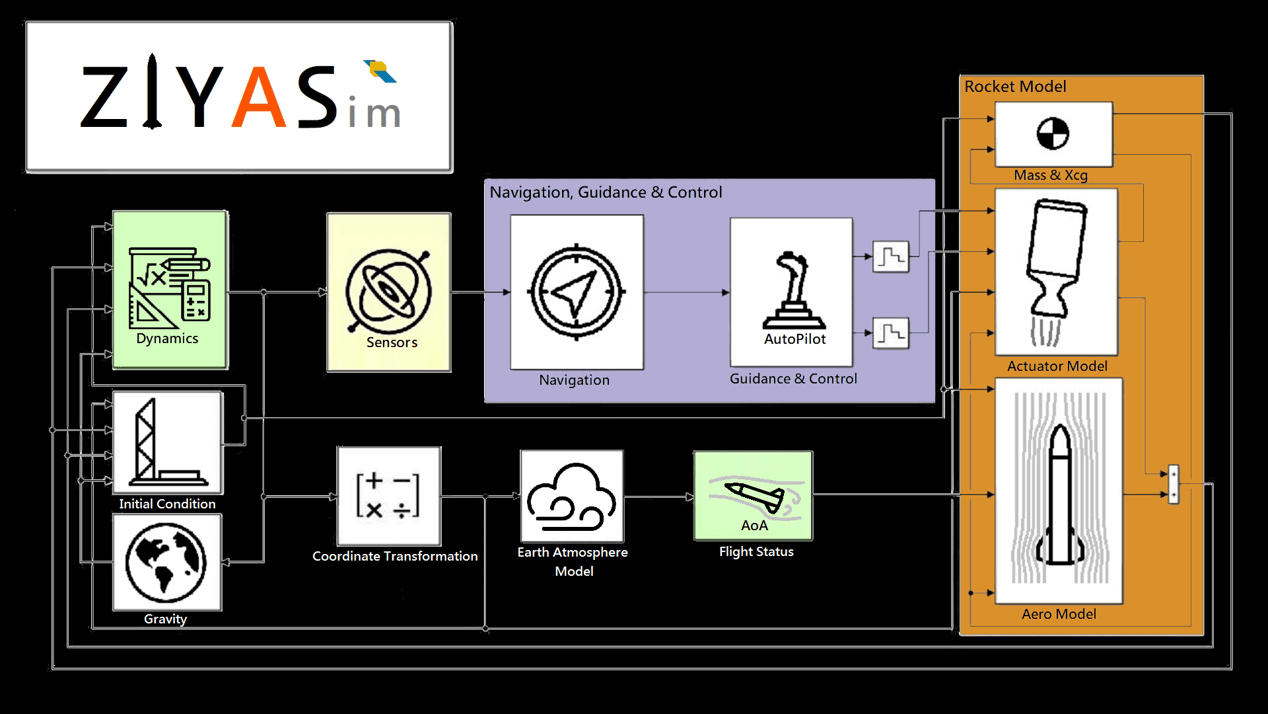
SYSTEM ENGINEERING
Mission Analysis 6-DOF Simulation Tool
The in-house developed mission analysis simulation tool is able to perform complex 6-DOF simulations under various flight conditions. This tool which applies the Newton's 2nd Law can consider the effects of aerodynamic force, gravity force, guidance, navigation and control (GNC) and realistic wind models during a detailed flight modeling. It is the most important tool for deciding the rocket system configuration, which leads to other subsystem's specifications.

Web-based Visualization System
In order to monitor and record important information from the rocket. A long range wireless communication system is implemented using software define radio and Nvidia TX2. It will help the rocket transfer the real time video stream, critical and non-critical data to the ground station for further analysis.
Propulsion
Sam-á-Tsiáu Engine
- ● Engine type: Hybrid rocket engine
- ● Thrust level: 1.2 KN (Sea level)
- ● Full thrust burning time: 60 s
- ● Oxidizer: 90% H2O2
- ● Fuel: Thermoplastic
- ● Chamber pressure: 40 barA
- ● Sea level Isp: 242 s (Nozzle expansion ratio: 6.25)
- ● Vacuum Isp: >300 s (Nozzle expansion ratio > 40)
- ● Engine ISP efficiency: 98.6%
- ● Deep throttling capability: 20%
- ● Flexible re-ignition
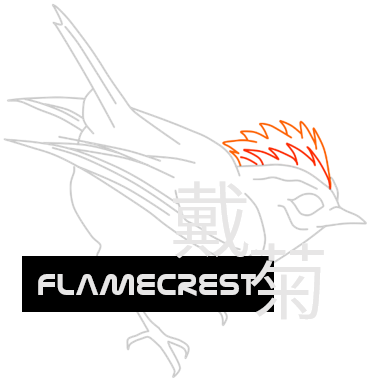
Tsuâ-Ing Engine (Flight test version)
- ● Engine type: Hybrid rocket engine
- ● Thrust level: 13 KN (Sea level)
- ● Full thrust burning time: 60 s
- ● Oxidizer: N2O+O2
- ● Fuel: Thermoplastic
- ● Sea level Isp: 220 s (Nozzle expansion ratio: 6.25)

Thrust Vector Control (TVC) System
- ● Swing angle: +/- 20˚
- ● Angular accuracy: < 0.05˚
- ● Angular rate: > 15˚/s

Rocket Engine Composite Nozzle
- ● Endurable, light-weight and scalable nozzle
- ● Housings: Metal
- ● Composite ablative liners: Phenolic based materials
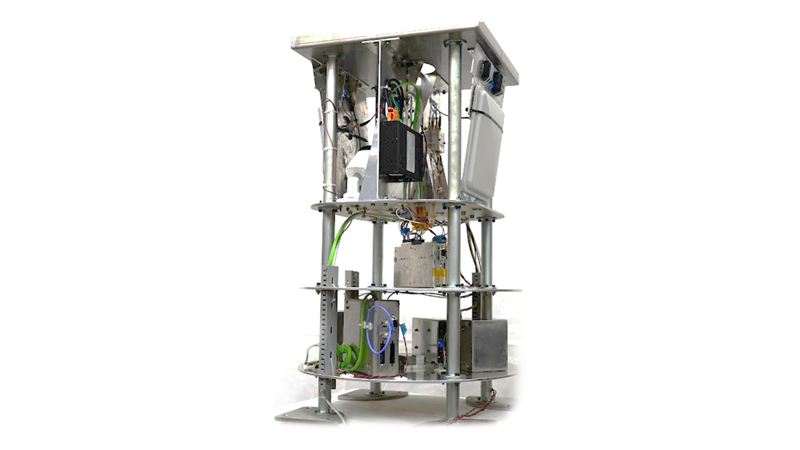
AVIONICS
ARRC builds up the rocket avionic system with high-performance and integrated techniques, which can cope with the flight control and telecommunication requirements under the highly dynamic environment.This system is modularized in design and allows easy customization of different functions and flexible mission requirements. The flight software (FSW) is developed on a hard real-time operating system (Hard RTOS) which is developed from the Linux OS.
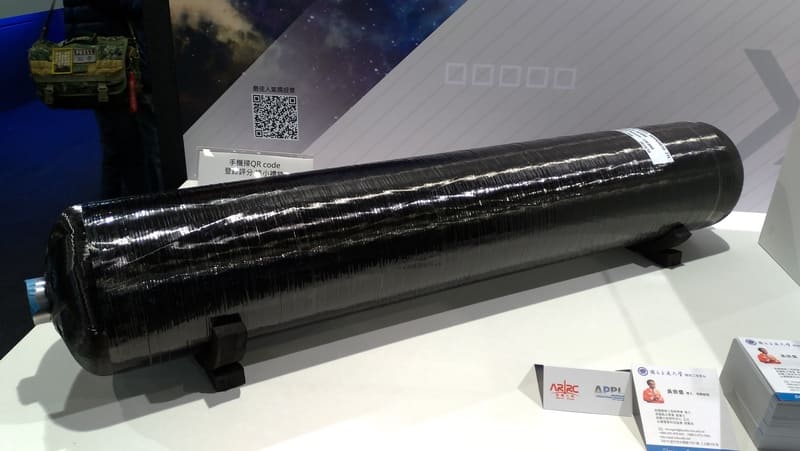
Structure
We have adopted light-weight structure strategy for making HTTP-3A as light as possible yet strong enough for surviving from the harsh flight environment in atmospheric and space environments. Many CFRP (carbon fiber reinforced plastic) and other light-weight materials such as aluminum alloy are employed wherever they can be. Numerous static and dynamic structure analyses are performed to optimize the design of the structure configuration of the rocket before fabrication. Many advanced CFRP composite pressure tanks for storing oxidizers and motor outcasings are designed, built and tested throughout this project.
Composite Cylinder
- ● Carbon fiber winded
- ● Metal or thermoplastic liner
- ● Working pressure: 60 barA

Recovery system
There are 4 sets of pilot chute which are designed with a working diameter of 1.8 meters. Not only are they able to pull out the main parachute, they can also act as a drag chute to reduce the speed.
With 2 sets of main parachute designed based on T-11 parachute, these parachutes have a 5.4 meter working diameter and are able to reduce the landing speed of HTTP-3A rocket to under 7 m/s.
- ● Main chute: Cruciform parachutes
- ● Drogue chute: Pulled-down apex (PDA)
COMING SOON
Payload System & Telecommunication System